1、 Failure to evenly feed
In fact, the reason why most
screw conveyors are prone to material blockage failures is due to the operator's failure to strictly operate according to operating standards. When starting, the operator should ensure that there is no load and the feeding is uniform. When the conveyor is empty, it must be stopped and cannot run empty. In addition, if the material is added suddenly during the feeding process, it can easily cause blockage and increase the wear of the conveyor. Therefore, it is necessary to gradually increase the feeding process and gradually reach the rated conveying capacity. Taking my friend's factory as an example, it was found through inspection that the reason for the blockage of the screw conveyor was due to the tight schedule and limited manpower at the time. The new employees were feeding too much, resulting in the blockage.
Solution: Evenly feed or install a vibrating feeder.
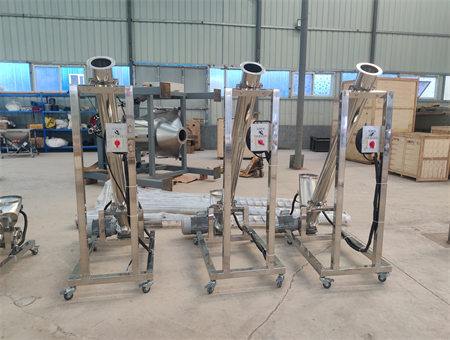
2、 Failure to consider conveying materials, conveying capacity, conveyor speed, motor power, etc
When selecting a
screw feeder, it is usually necessary to consider the conveying materials, conveying capacity, conveyor speed, motor power, etc. If the selected conveyor and the materials to be conveyed do not match the achieved effect, it is also easy to cause material blockage problems in the conveyor.
Solution: Choose the conveying capacity, conveyor speed, motor power, etc. that match the conveyed materials.
3、 Failure to clean up impurities in a timely manner after conveying materials
After the material is transported by the
screw conveyor, there must be impurities inside the machine. If necessary cleaning is not carried out, it can also cause residual large impurities or fiber impurities to cause blockage.
Solution: To reduce the occurrence of material blockage, the interior of the machine should be cleaned in a timely manner after the conveying of materials.
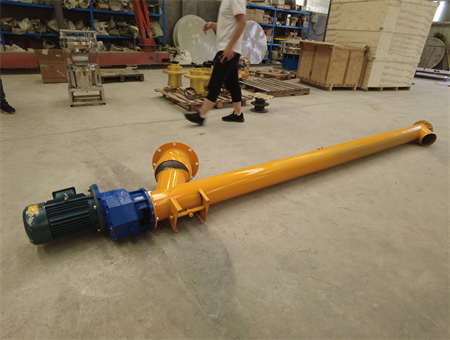
4、 The lateral dimension of the bearing is too long
This point is actually easy to overlook, after all, no one would have expected that excessive lateral dimensions of bearings can also cause material blockage. However, it has been proven that excessive lateral dimensions of conveyor bearings can easily lead to material blockage problems.
Solution: To reduce the occurrence of material blockage faults, the horizontal size of the suspension bearing should be minimized as much as possible.
In addition to the above methods, silo level sensors and blockage sensors can also be installed to achieve automatic control and alarm; Increasing the discharge port or lengthening the end of the material groove can effectively solve the problem of poor discharge, and a small section of counter rotating blades can also be installed at the end of the discharge port material groove. These can effectively prevent material blockage at the end.